Leading Strategies for Optimizing Steel Fabrication Processes for Maximum Effectiveness
In the world of steel construction, the pursuit of efficiency is a continuous objective that drives market professionals to discover cutting-edge methods and innovations. As the need for accuracy and speed intensifies, companies are urged to review their fabrication processes constantly. From precise format intending to accepting advanced technologies, the pursuit for optimal effectiveness in steel fabrication includes a multifaceted strategy. By implementing top methods tailored to maximize procedures, companies not only enhance efficiency however also raise the high quality of their output. Let's discover just how these methods can change steel manufacture processes, leading the means for extraordinary efficiency and competitiveness in the sector.
Effective Layout Preparation
In the realm of steel manufacture processes, reliable and calculated design preparation plays an essential duty in streamlining production workflows and taking full advantage of operational efficiency. The design of a steel construction facility directly affects the effectiveness of operations, material flow, and employee performance. By thoroughly creating the arrangement of equipment, workstations, storage space locations, and product handling devices, business can substantially lower unnecessary motion, decrease material taking care of times, and optimize the total production procedure.
An efficient design plan thinks about factors such as operations series, proximity of workstations, product handling courses, and security guidelines. It aims to develop a structured and sensible circulation of tasks from basic material intake to the final item dispatch. Through reliable layout preparation, firms can eliminate traffic jams, lower production downtime, and enhance the overall operational effectiveness of the steel manufacture procedure.
Furthermore, a well-thought-out format plan allows far better application of available area, improved interaction between employees, and enhanced security practices within the facility. Generally, investing time and resources in establishing a reliable format strategy can produce substantial advantages in regards to enhanced performance and cost financial savings for steel manufacture organizations.
Advanced Cutting Technologies
Using cutting-edge innovations in steel fabrication procedures boosts accuracy, performance, and overall production high quality. In addition, plasma reducing innovation has also revolutionized steel construction by enabling swift and exact reducing through electrically conductive materials. By incorporating these sophisticated reducing technologies right into steel fabrication procedures, makers can significantly raise performance, reduce manufacturing times, and eventually enhance the top quality of their products.
Automated Welding Equipments
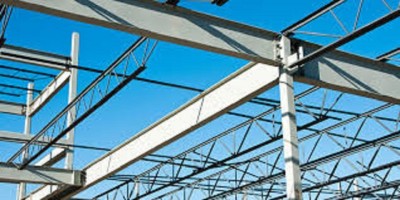
One of the key benefits of automated welding systems is their capability to preserve a high level of accuracy throughout the welding procedure. The accuracy used by these systems guarantees that welds are consistent and fulfill the needed specs, resulting in more powerful and a lot more reliable metal structures. Furthermore, automated welding systems minimize the threat of human mistake, leading to less issues and rework.
Furthermore, these systems can handle intricate welding tasks easily, consisting of welding in limited spaces or on bent surfaces. This adaptability makes automated welding systems ideal for a wide variety of steel construction applications, from large commercial projects to elaborate personalized designs. In general, the application of automated welding systems in steel construction processes substantially enhances performance, top quality, and overall project results.
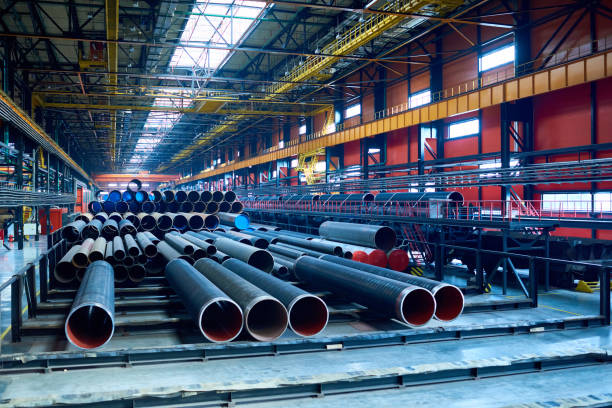
Stock Administration Solutions
Enhancing operational effectiveness and enhancing procedures, efficient stock administration services play an important function in enhancing steel construction operations. By executing robust inventory monitoring systems, steel manufacture firms can make sure that the ideal materials are available when needed, decreasing disturbances and hold-ups in production schedules. Making use of innovative software application services allows for real-time tracking of supply levels, enabling exact projecting of material requirements and protecting against stockouts or overstock scenarios.
Additionally, inventory monitoring options help in reducing lugging costs related to excess supply and improve cash money flow by aligning supply levels with real demand. By classifying materials based upon usage frequency and urgency, fabricators can focus on procurement and storage room other allotment, better improving operational effectiveness. Additionally, carrying out barcode or RFID technology promotes accurate supply tracking and streamlines the surveillance of material activities within the facility.
Continual Refine Improvement
To build on the gains made through efficient supply management remedies, the focus now changes towards driving constant procedure improvement within steel construction procedures. Continuous process renovation is a systematic method targeted at enhancing effectiveness, minimizing waste, and increasing overall high quality throughout the manufacture process. By executing a society of continual improvement, steel fabrication business can determine traffic jams, streamline workflows, and enhance sources to maximize productivity.
One key element of constant procedure renovation in steel manufacture is the normal review and analysis of production processes. This involves event Your Domain Name feedback from staff members, keeping an eye on crucial efficiency indications, and recognizing locations for improvement. By leveraging data-driven understandings, firms can make enlightened choices to drive purposeful adjustments that favorably affect procedures.
Additionally, embracing lean manufacturing principles can considerably contribute to process improvement in steel fabrication. steel fabrication melbourne. Methods such as value stream mapping, 5S company, and Kaizen occasions can assist get rid of non-value-added activities, systematize procedures, and promote a culture of development and continuous understanding within the company
Conclusion
To conclude, maximizing steel fabrication procedures for optimal efficiency needs cautious preparation, utilizing sophisticated reducing modern technologies, implementing automated welding systems, handling stock properly, and continuously improving processes. By integrating these recommended you read approaches, manufacturers can improve efficiency, minimize expenses, and boost total efficiency in the steel fabrication industry.
Through effective design preparation, firms can eliminate bottlenecks, reduce production downtime, and enhance the overall operational efficiency of the steel construction procedure. metal fabrication melbourne.
Utilizing cutting-edge technologies in steel fabrication processes boosts accuracy, performance, and total manufacturing high quality. By integrating these sophisticated cutting technologies into steel manufacture procedures, makers can substantially boost effectiveness, decrease production times, and inevitably boost the high quality of their products.
Overall, the execution of automated welding systems in steel manufacture processes considerably improves performance, high quality, and general project end results.
One secret aspect of continual procedure improvement in steel manufacture is the normal evaluation and evaluation of manufacturing processes. (Alpha reo)